Advanced EDM for Precision Tooling
At Houston Plastic Products, we elevate precision tooling with our state-of-the-art Makino EDAF3 for Sinker EDM and Makino U3 for Wire EDM.
These advancements revolutionize tooling and underscore our commitment to plastic innovation, sustainability, and quality.
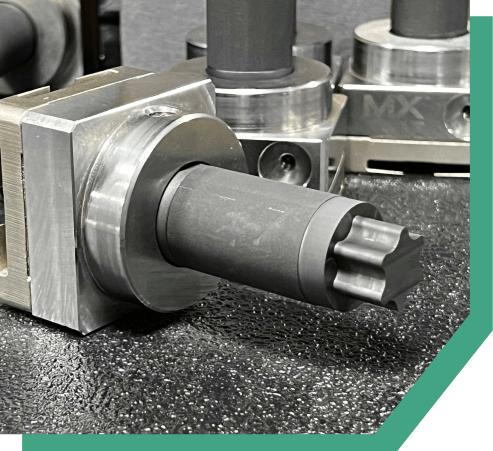
precision shaping for the toughest materials
Say goodbye to rapid tool wear from traditional subtractive machining. With electric discharge machining (EDM), we deliver precision cuts without direct contact, offering the following advantages:
<span data-metadata=""><span data-buffer="">enhanced durability
intricate design capabilities
superior surface finishes
reduced tooling costs
<span data-metadata=""><span data-buffer="">Achieving Precision, Durability, and Flawless Finishes.
Unmatched expertise for precision in plastic products
Sinker EDM offers precision cutting of conductive materials using controlled electric discharges, likened to a sculptor using micro-explosions instead of a chisel. This process utilizes tool and workpiece electrodes that generate intense heat, selectively vaporizing targeted material sections. The outcome is an exceptionally precise and surgical cut.
Wire EDM uses a charged electrode wire submerged in dielectric fluid to meticulously shape conductive materials without physical contact, ensuring no distortion during cutting. Its advanced control instruments enable intricate three-dimensional designs, making it ideal for crafting tight-tolerance parts, punch dies, and complex patterns. This technique is favored for thick plates, extrusion dies, and other precision tasks.
Complex specifications and tight deadlines demand quality and consistency.
HOUSTON PLASTIC PRODUCTS DELIVERS, EVERYTIME.
Trust Houston Plastic Products for your complex injection molding needs. Our Design for Manufacturability (DFM) expertise, rigorous safety standards, and exceptional quality control protocols allow us to deliver excellence consistently.
Partner with Houston Plastic Products for efficient custom solutions that enable you to achieve your sustainability goals without sacrificing quality.
Frequently Asked Questions
Selecting between Sinker EDM and Wire EDM requires careful consideration of workpiece needs: cuts from above suit Sinker EDM, while side cuts favor Wire EDM. Sinker EDM is typically chosen for molds, while Wire EDM excels in creating punches. Additionally, Wire EDM offers speed, ease, and low maintenance.
We are proud to offer electric discharge machining services through the use of our Makino EDAF3 machine for Sinker EDM and Makino U3 for Wire EDM.
Electric discharge machining can take as little as a few hours, depending on the complexity of the design. It is much faster than traditional machining.
EDM is much more cost-effective than traditional machining, providing high quality for smaller budgets.